Composites
For this week the assignment was to do something with composites. Thinking about the strength of 3D printed models I decided to experiment with hollow 3D printed objects filled with silicone, as an attempt to improve mechanical properties of PLA models.
I use a MakerBot Replicator 2X for print a 3D model of an ASTM test specimen downloaded from GrabCAD.com (ASTM D638-10 Type IV Tensile Specimen).
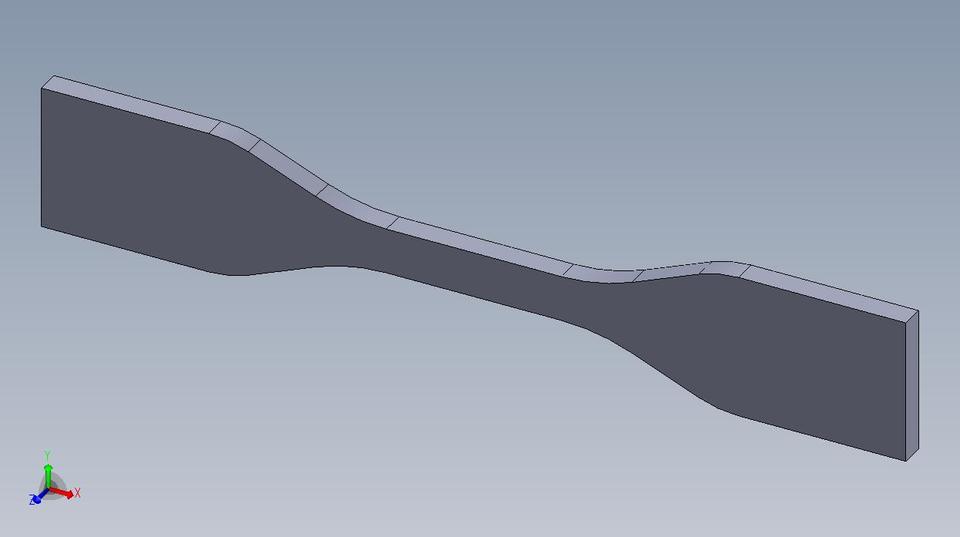
This model was slightly modified in SolidWorks for achieve a cross sectional area of 6mm x 6mm. Parameters for 3D printing were 0% infill, 0.2 mm of layer thickness, and 4 layers. I used ABS and the total time for print 3 specimens was 1 hour approximately.


For filling purposes, each specimen was drilled (2 holes) and filled with clear silicone.


The specimens were let apart for 24 hours for a full cure time, then, they were tested on an Universal Testing Machine.
The parameters for this tensile test were:
Units: SI
Geometr. Form: Rectangular
Number of specimens: 3
Number of chanels: 2
Machine Type: -------
Machine Control: STANDARD
Data Frecuency: 0.500000 point/sec
Extensometer: Off
Cross-piece Speed: 5.00000 mm/min
Second Speed: -------
Temperature: 24 °C
Humidity: 55 %
Reason for Test completion: test stopped by the user
Width: 6.2900000 mm
Thikness: 5.8899999 mm
Initial Length Specimen: 113.9999924 mm
Initial Length ext:60.0000000 mm
And the results of the test are shown in this graph:
In same way, 3 specimens of ABS were printed with 100% infill and tested.
The parameters for thsi test were the same for composite specimens, and the results are shown in following graph:
Comparing values of force and extension in maximum force point:
Specimens | Mean Maximum Force | Mean Extension at Maximum Force |
---|---|---|
ABS+Silicone | 0.685 kN | 2.33 mm |
ABS | 0.725 kN | 1.33 mm |
We can observe that silicone increases the elongation to material but with a slight diminution in material strength.
Notes
Section of failure for full ABS specimen shows that a 100% infill is not real:
In the composite specimens we observed that in the last printed layer of material, some filaments were bended inwards due to its melting state during 3D printing process. This condition helped to silicone infill join with ABS. In other places inside the specimen, the internal walls were so flat that silicone could not adhere to the inner walls.
Future tests will require an internal design of specimen that promote creation those inwards bended filaments for a better integration between silicone and ABS.
Composites
- Computer Aided Design
- Computer Controlled Cutting
- Electronics Production
- 3D Scanning and Printing
- Electronics Design
- Computer-Controlled Machining
- Embedded Programming
- Molding and Casting
- Input Devices
- Composites
- Output Devices
- Networking
- Mechanical Design
- Interface and Application Programming
- Applications and Implications
- Business Models
- Project Development